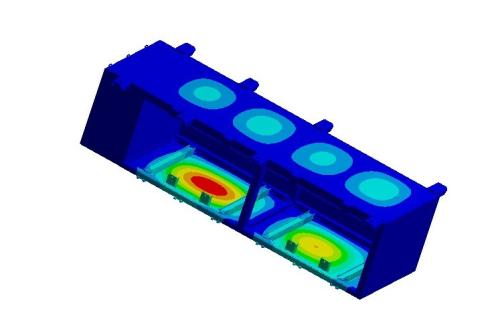
為了適應國民經(jīng)濟快速發(fā)展的要求,鐵路客運已經(jīng)6次提速。客車提速后,迫切需要提高貨物列車的運行速度,并改善車輛運行品質(zhì)。當前,我國主型貨車轉向架是由2個側架和1個搖枕組成,又稱3大件式轉向架。這種轉向架結構簡單,檢修方便,但簧下質(zhì)量大,抗變形剛度小,其較大的輪軌動力作用和蛇形失穩(wěn)問題制約貨物列車的運行速度進一步提高。
為提高貨物列車的運行速與改善運行品質(zhì),焊接H型整體構架式轉向架也是目前世界上較為成熟、應用較多的一種快速貨車轉向架。某貨車廠開發(fā)設計4D軸焊接構架式轉向架用于載重120 t長大平車的運輸。轉向架軸重為采用變摩擦減振器,軸箱彈簧為二級剛度。同時,采用常接觸雙作用彈性旁承,增大轉向架與車體之間的回轉阻尼,抑制轉向架蛇行運動。本文采用國際鐵路聯(lián)盟UIC510-3規(guī)程和熱點應力評價方法,并實測動應力譜,對新型4D軸貨車轉向架焊接構架的疲勞強度和疲勞壽命進行了分析和評價。
構架用材為Q345E鋼,彈性模量為206 GPa,泊松比為0.3。取整體構架結構進行有限元分析建模,各軸箱導框采用4節(jié)點4面體單元Solid45離散,剩余部分采用4節(jié)點殼單元Shell63離散。整個構架模型共離散為166650個單元、163204個節(jié)點。
在疲勞強度計算中,主要考慮垂向、橫向和斜對稱3種載荷。其中,斜對稱載荷是將車輪上的扭轉按5‰軌道扭曲量進行考慮。運營載荷工況組合,其中Fz為垂向靜載荷,F(xiàn)y為橫向載荷,α=0.23為橫向動荷系數(shù),β=0.3為垂向動荷系數(shù)。
構架通過軸箱導框和軸箱彈簧與軸箱相連,因此在構架軸箱導框彈簧支撐處施加三向彈性位移約束。
在材料的疲勞極限用應力幅值表示時,疲勞極限隨應力比的改變而改變。因此,可以根據(jù)不同的應力比得到的疲勞極限,在相同的壽命上畫出疲勞極限圖。Goodman疲勞極限圖是進行強度評估時應用最為廣泛的等壽命曲線。
計算結果在構架結構模型上分別施加表1中所列的7個模擬運營載荷工況,計算各工況下構架結構的應力,然后再計算這7個工況中任意2個工況下的應力差值和平均應力(兩者代數(shù)和之半),即可得到整個構架的動應力幅值和平均應力。表2給出第2和第7、第4和第7、第3和第4組合工況下大應力部位的動應力幅值及平均應力,這3種組合工況易導致構架出現(xiàn)較大動應力。動應力較大的部位為側梁下蓋板與導框連接區(qū),枕梁上下蓋板與側梁連接區(qū)。其中,側梁下蓋板與導框連接區(qū)為E級焊縫,而枕梁上下蓋板與側梁連接區(qū)為D級焊縫。將表中列出的構架大應力區(qū)域的動應力幅值和平均應力,點入Q345E鋼焊接接頭的Goodman圖中。可以看出,整個構架的疲勞薄弱部位為側梁下蓋板與軸箱導框的焊縫連接區(qū),發(fā)生在工況4和7及3和4的組合作用下。
側梁下蓋板與導框連接區(qū)枕梁上蓋板與側梁連接區(qū)枕梁下蓋板與側梁連接區(qū)熱點應力法熱點應力指最大結構應力或“結構中危險截面上的點應力”。焊接結構中熱點一般選焊趾處,因為此部位最容易產(chǎn)生疲勞裂紋。國際焊接學會建議對焊接結構的疲勞損傷進行評定時,應進行熱點應力分析,采用最可能發(fā)生疲勞破壞部位處的應力幅值作為疲勞設計依據(jù)。
熱點應力由膜應力和彎曲應力兩部分組成,是構件表面熱點處膜應力和彎曲應力之和的最大值,不包括焊趾處局部缺口引起的非線性應力峰值,這也是熱點應力和缺口應力的區(qū)別。熱點應力呈線性分布,一般用外推的方法得到。為避開非線性應力峰值的影響,外推測量點應該距離焊趾足夠的距離,一般在距離焊趾0.4t(t為板的厚度)處。因為此處非線性應力峰值基本消失,外推點應該從這個位置開始,國際焊接學會推薦的外推方法為在距離焊趾。
由于構架受載復雜,因此需要研究將復合應力轉化為單向等效應力的方法,以便得出沿焊縫垂直方向的結構應力分布。
專業(yè)從事有限元分析公司│有限元分析│CAE分析│FEA分析│技術服務與解決方案
杭州那泰科技有限公司
本文出自杭州那泰科技有限公司m.dlghtz.com,轉載請注明出處和相關鏈接!